Технологический процесс сварки: особенности
Сварка применяется довольно широко как в коммерческих, производственных целей, так и для выполнения мелкого ремонта в частном строении или на даче. Оборудование, расходные материалы для сварочных работ предлагаются потребителю в специализированных магазинах и являются доступными. Процесс выполнения сварочного соединения зависит от вида сварки. Но наибольшее распространение приобрела дуговая сварка. Именно ее чаще всего применяют в быту. Но от правильного исполнения технологического процесса сварки зависит качество, надежность сварного соединения, а также безопасность самого работника.
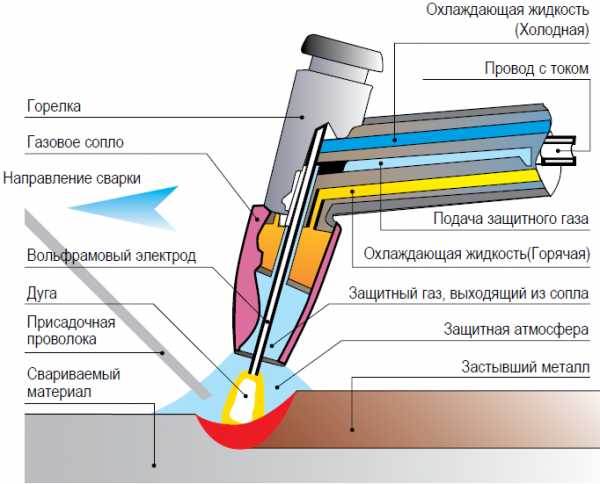
Процесс сварки электродом.
Подготовка и комплектация
Для того чтобы выполнить сварной шов при помощи ручной дуговой сварки, необходимо подготовить расходные материалы, маску для сварочных работ. Напряжение в электросети при этом должно соответствовать номинальным показателям, которые требуются для нормальной работы сварочного оборудования. Если есть прочие агрегаты, в работе которых нет необходимости, то их желательно не использовать в процессе дуговой сварки. Это применимо для бытового использования дуговой сварки. На производстве электрические сети выполняются с запасом нагрузки, поэтому работа сварочного оборудования в процессе дуговой сварки не вызовет нежелательных последствий.
Схема классификации сварных швов.
Кроме того, в наличии должны быть:
- Сварочный аппарат, который состоит из реостата, держателя, заземляющего кабеля.
Реостат, который предоставляет возможность изменять подаваемый ток. Этот параметр должен соответствовать типу стали, из которой изготовлены металлические детали для сварки. Величина подаваемого тока должна зависеть от того, насколько глубокой должна быть сварочная ванна, каким будет резаный шов, от степени стягивания, методов наплавления.
Кабель, который используется для такого соединения, может состоять из 1, 2, 3-х жил. Главное, чтобы кабель был рассчитан на предполагаемые нагрузки, причем с запасом. Иначе возможно его повреждение непосредственно в технологическом процессе сварки. Заземляющий кабель необходим для того, чтобы при соприкосновении электрода со свариваемой поверхностью замыкался контур, образовывая тем самым дугу для выполнения сварочных работ.
- Расходные материалы.
Общая характеристика свариваемости материалов.
К таким материалам можно отнести несколько электродов. Их количество определяется размером свариваемого шва. В зависимости от типа и состава стали, из которой выполнены свариваемые детали, выбирают тип электрода. Состав покрытия электрода, условия правильного хранения и прочие требования, которые предъявляет производитель к потребителю, должны быть указаны на упаковке. Пользователю необходимо ознакомиться с ними и четко выполнять требования, что обеспечит хорошую производительность данного расходного материала.
- Проволока для сваривания.
Марка проволоки, химические компоненты, которые находятся внутри нее, также определяются материалом, из которого выполнены элементы для сварки. Все обозначения и область использования проволоки должен указывать производитель на упаковке. Этот расходный материал должен в точности соответствовать марке стали, иначе сварное соединение будет непрочным или его невозможно будет выполнить.
- Если сварочный технологический процесс требует применение флюса, то смесь должна в полной мере защищать рабочее свариваемое пространство.
Некоторые виды флюсов могут применяться только при специфических работах, если элементы для выполнения сварки имеют сложный состав и особые требования по качеству полученного соединения.
- При сварке в особых условиях или при определенных металлах может потребоваться газ.
Аргон, гелий и их смеси, не влияя на химический состав сварной спайки, тем не менее ограничивают доступ кислорода в рабочую зону.
Некоторые особенности
Принцип газовой сварки.
При выполнении сварочных работ необходимо соблюдать требования техники безопасности, благодаря которым сварщик защищен от вредного воздействия брызг металла, ожогов для глаз. Такую защиту способна обеспечить маска сварщика, которая продается в специализированных магазинах. Специальное стекло, которое размещается в маске, надежно защищает глаза. Необходимо следить за тем, чтобы оно не было повреждено или поцарапано.
Любое повреждение стекла может привести к ожогу роговицы глаза сварщика или может ослепить его на время.
Если деформация стекла произошла во время выполнения работ, их надо прекратить до его замены.
Способы и режимы газовой сварки: А — ванночками; Б — по отборочным кромкам.
Если при сварке произошла временная потеря зрения, то работа приостанавливается до полного его восстановления. Кроме маски глаза можно защищать очками. Но они не обеспечивают полноценной защиты головы и глаз в связи с тем, что сварка основана на создании дуги между электродом и деталью, для возникновения которой необходимо прохождение электрического тока по кабелю.
Для того чтобы защитить сварщика от возможных поражений током при повреждении кабеля, необходимо все работы производить в специальных перчатках, выполненных из резины. Кроме того, перчатки должны быть сухими и без повреждений. Кабель, который соединяет держатель и сварочный аппарат, нельзя протягивать через лужи, талый снег. При несоблюдении этого условия техники безопасности возможен выход из строя сварочного аппарата, а кроме того, сварщик может получить удар электрическим током.
Чтобы обеспечить качественное сварное соединение, которое в дальнейшем прослужит не один год, необходимо на подготовительном этапе обеспечить:
- Бесперебойное электрическое питание для сварочного аппарата.
Углы наклона мундштука горелки при сварке стали различной толщины.
При этом номинальные характеристики сети должны соответствовать предъявляемым требованиям для сварочного оборудования, которое используется в процессе работ.
- Целостность расходных материалов, правильность их хранения, бережное транспортирование. Это позволит выполнить шов ровный и надежный.
- Кабель, соединяющий сварочный аппарат и держатель должен быть целым, без повреждений изоляционного слоя.
При обнаружении такого дефекта кабеля, он должен быть немедленно заменен на другой. При эксплуатации поврежденного кабеля сварочный аппарат может сломаться, а сварщик рискует получить ожоги электрическим током.
Техника сварочных работ
Принцип электродуговой сварки.
После того как выполнены все требования по технике безопасности, подготовлены материалы и детали, можно приступать к выполнению сварочных работ.
На сварочном аппарате надо установить рабочее значение тока, при котором будет производиться сварка. Ее определяют исходя из марки электрода, типа стали, вида сварного шва, месте его расположения на металлической конструкции и в пространстве. Чтобы образовалась дуга, необходимо электрод поднести к начальному месту для сварки. При этом электрод и металл должны быть перпендикулярны. После того как они соприкоснутся, электрод приподнимают на 2-5 мм от металла, в результате чего образуется дуга.
Такой процесс получения дуги используется для начала шва. Когда необходимо зажечь дугу уже на этапе выполнения шва, когда сварная ванна уже образовалась, этот технологический процесс выглядит несколько иначе. Чтобы шов был непрерывным, дугу надо зажигать прикосновением к ней электрода, немного отступив от места, где дуга оборвалась по шву. Если сварщик обладает опытом, дуга обрывается редко, что позволяет обеспечить целостность сварного шва.
Виды сварных соединений.
От того как в пространстве будет располагаться будущий сварной шов, зависит способ размещения электрода и его позиция. Швы могут располагаться внизу, на вертикальной поверхности (вертикально, горизонтально), на потолке. Элементы, которые необходимо соединить в вертикальной плоскости, сваривают, двигаясь сверху вниз. При нижнем размещении сварного соединения электрод должен быть наклонен в направлении сварки в вертикальной плоскости, а варят при этом «к себе» или «от себя».
Движения электродом по свариваемой поверхности, которые выполняет сварщик, могут иметь различную траекторию. Она зависит от размера шва, типа стали свариваемых элементов, а также от мастерства сварщика. Движения могут способствовать прогреву корней шва, прогреву только одной из кромок шва или п двух кромок.
Устройство сварочного инвертора.
От того каким образом происходит движение электрода по свариваемой поверхности, будут зависеть деформации сварного соединения, и напряжения, которые в после окончания работы будет испытывать шов. Сами движения электродом должны быть поступательными и достаточно плавными. Однако остановки при сварке могут образовывать наплывы, а частое зажигание дуги лишние повреждения окружающей поверхности.
Кроме того, сами сварные швы могут быть длинными, средними и короткими. Размеры их составляют выше 1000 мм, более 350 мм и менее 1000 мм, менее 350 мм соответственно. Если шов должен быть значительных размеров, то его выполняют несколькими отрезками, чтобы не допустить значительного прогревания металла кромок и повреждения поверхности металлической детали (прожига). При этом необходимо учитывать, что шов должен оставаться без отверстий, быть целым и аккуратным. Количество и размер отрезков для длинного шва зависят от его размера и чаще всего делится на 4-5 равных частей, если это позволяет сделать конструктивные особенности детали. Если шов короткий, то началом для него может служить любая удобная для подступа сторона. При средней длине шва его выполнение начинают с середины и постепенно движутся к краям. При этом направление движения обусловлено только конструктивными особенностями детали.
Практические рекомендации
Швы могут выполняться в один проход, и тогда такую спайку называют однослойной. Если сварной шов образовался путем нескольких прохождений электродов, то это многослойный шов. Соединение, которое образовалось в процессе однослойной сварки, не является пластичным и выглядит достаточно грубо. Это связано с тем, что металл в районе выполнения соединения был сильно перегрет. Но при этом именно шов, полученный в один проход экономичен и производителен.
Многослойная сварка образует аккуратный шов в результате того, что каждый проход прогревает только определенный участок металла. При этом выполняется тонкий шов, который при втором проходе увеличивается незначительно. При многослойной сварке слои могут располагаться последовательным или каскадным образом, горкой. При последовательном способе каждый из следующих слоев накладывается на предыдущий только после того, как будет выполнен полностью проход по всему шву.
Каскадным способом и «горкой» пользуются при сваривании толстых слоев металла. При любом из способов многослойной сварки один проход должен быть выполнен особенно тщательно, от этого зависит прочность полученного соединения.
Преимущества и недостатки ручной дуговой сварки
Основным преимуществом такого типа сварки является простота и возможность выполнить небольшие швы не только сварщику в процессе работы. Бытовые сварочные аппараты можно использовать для мелких каждодневных нужд. Дуговая сварка может применяться в конструкциях любой сложности и положении. При этом необходимо обеспечить безопасность и надежность сварочного оборудования. Практически все металлы могут быть скреплены такой сваркой. Важно только правильно подобрать силу тока и расходные материалы. Дуговую сварку можно использовать практически при любой погоде за исключение дождя и снега. Но при сырой погоде или большой влажности работы необходимо выполнять аккуратно, а оборудование перед использованием тщательно проверять.
К недостаткам можно отнести негативное влияние на сварщика, которое образуется при воздействии на него электромагнитных волн. Большую роль в получении качественного и прочного шва играет опыт сварщика, его мастерство. При отсутствии навыков работы с дуговой сваркой могут образовываться дыры и прожоги, которые трудно заделывать в дальнейшем.
Даже в современных условиях дуговая сварка является самой применимой во всех видах производства, строительстве и быту.
moyasvarka.ru
Технология выполнения сварочных работ
Сварочные работы для начинающих
Технология выполнения сварочных работ не представляет большой сложности для освоения. Чтобы научиться пользоваться сваркой в быту, достаточно нескольких уроков и обязательно практические занятия. Что необходимо для работы сварочным аппаратом:
- аппарат для сварки;
- сварочные электроды;
- защитная маска;
- спецодежда;
- плотные рукавицы;
- обувь.
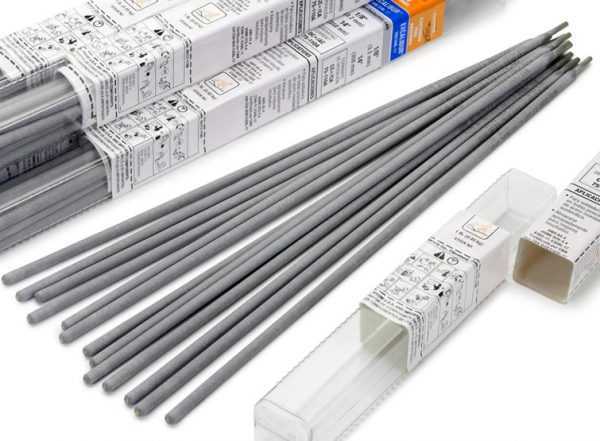
Электроды для выполнения сварочных работ
Теория электросварки
Чтобы быстрее научиться выполнять сварочные работы, необходимо иметь представление о теории электрической сварки. Сваривание металлов происходит за счет теплового действия электрической дуги между свариваемым металлом и электродом. Мощность дуги зависит от тока через нее, который в свою очередь зависит от напряжения и расстояния между электродом и деталью.
Важнейшей характеристикой сварочного аппарата является его вольтамперная характеристика. Иначе ее еще называют внешней характеристикой. Она показывает зависимость тока дуги от напряжения.
На рисунке ниже показаны несколько типов характеристик.
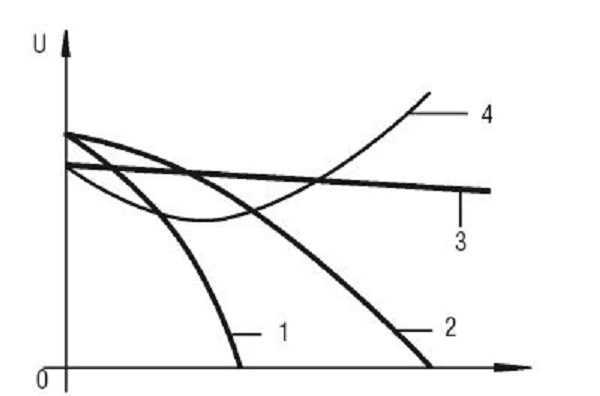
График внешних характеристик сварочного аппарата
Для ручной электросварки используются аппараты, характеристики которых соответствуют линиям 1 и 2. Это крутопадающая и пологопадающая характеристики. Как видно из графиков, сварочный ток у крутопадающей характеристики мало зависит от напряжения, а значит, и от расстояния между электродом и поверхностью. Сварочный аппарат с пологой и возрастающей характеристиками (линии 3 и 4) пригоден только для использования в автоматической сварке, где расстояние выдерживается очень точно. Для начинающих лучше использовать аппарат с крутопадающей характеристикой.
Сварочный аппарат имеет еще такую характеристику – напряжение холостого хода. От величины этого напряжения зависит легкость первоначального поджига дуги. Чем больше напряжение холостого хода, тем легче зажечь дугу. С другой стороны, в процессе сварки напряжение дуги намного меньше холостого хода.
Для облегчения поджига сварочный аппарат может дополняться специальным устройством – осциллятором, которое в момент поджига формирует на выходе напряжение в несколько тысяч вольт, но с малым током, подобно катушке зажигания автомобиля. При зажженной дуге осциллятор отключается.
Какой выбрать сварочный аппарат
Наиболее прост для начинающих инверторный сварочный аппарат (рис. ниже). Его достоинства:
- простота ограничения максимального тока;
- стабильность заданных параметров;
- легкость зажигания дуги;
- защита от перегрузки;
- низкий вес.
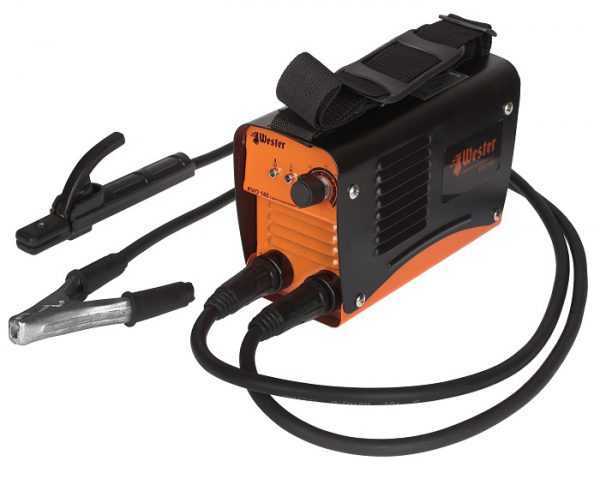
Инверторный сварочный аппарат
Сложнее работать с аппаратами переменного тока. Как правило, это обычный понижающий трансформатор большой мощности (рис. ниже), какой нетрудно сделать самостоятельно. Но у них есть такое достоинство, как высокая надежность. Нужно быть очень неумелым сварщиком и очень постараться, чтобы сжечь сварочный трансформатор весом пару-тройку десятков килограммов. Удобство работы такими аппаратами во многом зависит от качества их изготовления. Но, если научиться им правильно работать, то с другими проблем не возникнет точно.
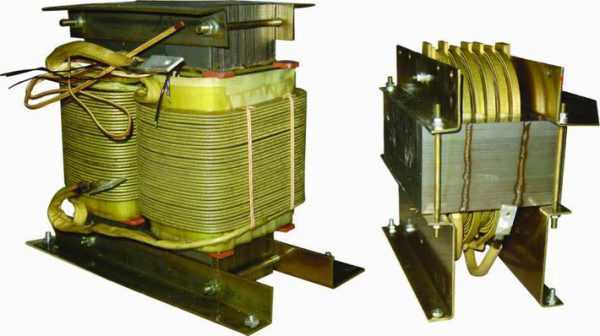
Сварочный аппарат – трансформатор
Чтобы правильно выбрать сварочный аппарат, необходимо учесть максимальный диаметр применяемых электродов и качество электропроводки.
При диаметре электродов 4 мм потребляемая от сети мощность составит порядка 4 кВт для инверторного аппарата и около пяти для сварочного трансформатора.
Сварочные электроды
Сварка производится сварочными электродами. Они изготавливаются из металлического провода, покрытого специальной обмазкой. От состава металла проволоки и материала обмазки зависит назначение электрода.
Существуют сварочные электроды для сварки низко,- и высокоуглеродистых сталей, чугуна, нержавеющей стали. Роль обмазки заключается в создании на поверхности расплавленного металла защитного слоя. Требования к материалу обмазки:
- температура плавления должна быть ниже, чем температура плавления металла;
- расплав обмазки должен иметь хорошую смачиваемость для равномерного покрытия;
- расплав должен поглощать кислород и не пропускать его к металлу;
- расплав должен растворять окиси.
Электроды различаются по типу тока. Одни предназначены для сварки переменным током, другие только постоянным.
Электроды для сварки постоянным током прекрасно работают на переменном. Электроды для работы на переменке, для сварки постоянным током не пригодны.
Техника сварки
Качество сварки зависит от соотношений толщины деталей и электрода, а также от величины сварочного тока. Обычно толщина электрода принимается равной толщине свариваемых деталей. Для более толстых электродов потребуется большее значение тока, что может привести к прожогам металла. Тонкий электрод при малом токе не прогреет металл, и качество сварного шва будет низким.
Оптимальная величина сварочного тока зависит как от диаметра электрода, так и вида производимых работ. Максимальный ток используется при выполнении горизонтальных швов, минимальный при работе с вертикальными и потолочными швами.
Особую трудность для начинающих составляет процесс поджигания дуги. Для этого сварочный электрод подносят к свариваемой поверхности и касаются ее легкими скользящими движениями. После поджига увеличивают расстояние между электродом и поверхностью. Оптимальная длина дуги должна составлять примерно толщину электрода. При меньшем расстоянии вся энергия дуги направлена на малую площадь, шов получится вогнутый, возможны прожоги металла. На краях шва металл, наоборот, не успевает прогреваться. Длинная дуга начинает «гулять» по поверхности, слабо прогревая место сварки.
Угол наклона электрода позволяет регулировать толщину сварочного шва. При вертикальном расположении весь расплавленный металл электрода концентрируется в области дуги. Однако при таком расположении трудно контролировать процесс сварки. Наклон в сторону, противоположную движению электрода дает возможность получить выпуклые швы, поскольку дуга отталкивает расплавленный металл, создавая наплывы на поверхности шва. Значительный наклон нежелателен, поскольку теряется контроль за дугой, она начинает сдувать капли металла. Оптимальным считается угол наклона электрода от 45 до 90 градусов.
Очень важна для качества сварки скорость перемещения электрода. При быстром передвижении металл не успевает полностью заполнить шов, который к тому же недостаточно прогрет.
Выбрать правильный угол и скорость перемещения можно только путем приобретения практического навыка.
Сварка постоянным током возможна при различных полярностях. Прямая полярность, когда электрод подключен к выводу отрицательной полярности, применяется для сварки с глубоким прогревом свариваемых деталей. Для работы с тонколистовым металлом необходима обратная полярность (электрод подключается к положительному выводу). При таком способе сварки большая часть тепла выделяется на электроде, вызывая его ускоренное плавление.
ТБ при сварочных работах
Сварочные работы считаются опасными, поскольку сочетают в себе сразу несколько факторов:
- высокое напряжение;
- высокая температура;
- мощное ультрафиолетовое излучение;
- высокое содержание вредных веществ в испарениях.
Сварочный аппарат характеризуется высоким напряжением холостого хода – до 80 В. Такое напряжение, даже при отсутствии повышенной влажности считается смертельно опасным (максимальное напряжение в нормальных условиях не более 42 В).
Температура расплавленного металла достигает нескольких тысяч градусов. При этом его текучесть очень высока. При некачественных электродах, неправильно выбранном режиме сварки или при сильном ветре брызги металла могут отлетать на несколько метров.
Электрическая дуга является мощным источником видимого и ультрафиолетового излучения. Кратковременное воздействие такого света не опасно, Просто требуется некоторое время для адаптации зрения к обычному освещению. А вот длительное наблюдение за дугой незащищенными глазами вызывает трудноизлечимые последствия, вплоть до помутнения хрусталика и отслоения сетчатки. Для защиты глаз применяются защитные сварочные маски (рис. ниже). Кроме защиты глаз, они защищают голову от брызг металла и шлака.

Сварочная маска для защиты глаз и головы во время сварки
Стекло маски не пропускает ультрафиолетовое излучение и в несколько раз ослабляет видимый свет, поскольку дуга – это близкорасположенный мощный прожектор. Сейчас в продаже имеется множество масок со специальными стеклами, которые меняют свойства в зависимости от яркости воздействия – «хамелеоны». При обычных условиях стекло абсолютно прозрачное. При зажигании дуги светопроницаемость стекла резко падает. Скорость затемнения составляет от нескольких миллисекунд до десятков микросекунд.
Для защиты от капель металла и шлака требуется одежда, материал которой не плавится от высокой температуры. Лучшими защитными свойствами обладает брезент, но в брезентовой одежде крайне неудобно работать. Достаточно использовать обычную спецодежду из хлопчатобумажной ткани. А вот рукавицы желательно выбрать поплотнее, поскольку руки находятся в непосредственной близости от места сварки.
Обувь для сварки должна иметь узкие голенища. Брюки должны быть поверх голенищ, чтобы предотвратить попадание туда брызг металла.
Дуговая сварка. Видео
Обучающее видео по дуговой сварке доступно ниже.
При горении электродов в воздух попадают пары металла и материала обвязки. В состав электродов входит немало химических соединений и многие из них представляют опасность при вдыхании. Поэтому зона проведения сварочных работ должна иметь хорошую вентиляцию. Запрещаются сварочные работы вблизи легкогорючих материалов (нефтепродукты, древесина), в сильный ветер и особенно во время дождя.
elquanta.ru
Виды сварочных работ и их особенности.
Сварка — это комплекс работ с применением специального сварочного оборудования, главной целью которого является создание прочного и неразрывного соединения между различными металлами посредством создания межатомных связей между ними. В основе сварки лежит термомеханическое воздействие.
Далеко не каждый знает о том, что существует свыше 40 видов сварочных работ, выполнение каждого из которых требует знания определенных нюансов и технологии, а также мер безопасности. Естественно, среди всех существующих видов сварочных работ можно выделить несколько наиболее популярных, которые пользуются широким спросом. Именно их мы с вами и рассмотрим:
1. Плазменная сварка. Этот вид сварки осуществляется посредством воздействия высокотемпературной плазменной струи на объект сварки. Основывается сварка на предварительном нагреве рабочего газа, его последующей ионизации и выпуске горячей струи на поверхность обрабатываемого материала. Многие по праву считают плазменную сварку самым прогрессивным, качественным и современным способом соединения двух металлов между собой. В каких областях промышленности применяется плазменная сварка? Да буквально во всех отраслях, в которых имеют дело с металлами: автомобилестроение, авиастроение, станкостроение, приборостроение и машиностроение.Что позволяет плазменная сварка? Начнем с того, что именно этот вид сварки существенно экономит энергетические ресурсы, повышает эффективность производства и качество производимой продукции, является первым этапом на пути к автоматизации производственных процессов предприятий различных отраслей. Безусловно, для достижения этих целей недостаточно лишь использовать плазменную сварку — необходимы также квалифицированные сварщики, которые смогут реализовать на практике все преимущества плазменной сварки.
Какими преимуществами обладает плазменная сварка? Во-первых, это высокий уровень мощности работы. Во-вторых — низкая чувствительность к дуговым колебаниям. В-третьих — возможность использовать плазменную сварку ко всем металлам и в любом из положений. И последними по счету, но не по значимости преимуществами являются высокая скорость плазменной сварки и значительный диапазон толщины резки. Посредством плазменной сварки металлы можно не только сварить, но и разрезать. В отличие от электродуговой сварки, плазменная сварка отличается возможностью ее контроля и наличием высококонцентрированной энергии сразу в эпицентре разогрева металлов.
2. Дуговая сварка. Это ручная сварка, которая производится с использованием металлических электродов. Этот вид сварочных работ пользуется широкой популярностью довольно давно, и на то есть свои причины. Во-первых, это легкость процесса сварки. Ничего сложного в нем нет — с ней справится даже начинающий сварщик без наличия значительного опыта работы. Второе преимущество дуговой сварки — мобильность. Вы не привязаны к сложному технологическому оборудованию, потому можете производить дуговую сварку даже в труднодоступных местах. Третье — возможность проведения сварочных работ в любых пространственных положениях. Четвертое — возможность быстрого перехода с одного сварочного материала к другому. Пятое — простота сварочного оборудования и легкость его перемещения. Шестое — возможность сварки разнообразных типов стали.
А есть у дуговой сварки какие-либо недостатки. Безусловно, есть. В противном случае иные способы сварки просто бы не применялись.
Итак, главными недостатками дуговой сварки являются:
1. Зависимость качества сварки от квалификации сварщика. Несмотря на то, что процесс сварки не очень сложен, он также имеет свои нюансы, которые должен знать и уметь делать сварщик. Самой большой трудностью ручной дуговой сварки является необходимость по мере оплавления подавать электрод в дугу, перемещать электрод вдоль шва, совершая при этом колебательные движения этим электродом, только уже поперек шва.
2. Наличие шлака в момент односторонней сварки с обратной стороны шва.
3. Невозможность сварщика регулировать скорость сварки и глубину плавки. Именно по этой причине очень часто не удается получить качественный шов во время сварки тонкого металла.
Слишком высокая зависимость качества сварки от индивидуальных особенностей и квалификации сварщика, а также невысокая производительность — вот какие главные недостатки дуговой сварки. Но что поделать — недостатками обладают даже самые, на первый взгляд, совершенные способы сварки.
3. Электрошлаковая сварка. Данный тип сварки используется при создании мощных турбин, барабанов, массивных станин и толстостенных котлов. Главным преимуществом электрошлаковой сварки является возможность сварки деталей любой, даже самой большой толщины за один проход. При этом чем больше толщина свариваемого материала, тем выше экономичность сварки, так как сама сварка производится без разделки кромок. Чаще используют данный вид сварки в случаях, когда требуется провести сварку материала начиная с толщины 100 и заканчивая 500 мм, но целесообразно ее использовать уже для металла толщиной от 50 мм.
Преимуществом электрошлаковой сварки является возможность ее применения для практически любого металла. Чаще всего она используется для сварки чугуна, алюминия, титана и меди повышенной толщины. Еще одно преимущество заключается в том, что для применения этого вида сварки не требуется производит настройку сварочной установки перед тем, как приступить к сварке следующего прохода, а также отсутствие обязательного удаления шлака. Кроме того, используя этот вид сварки, можно достичь высокой экономичности процесса и большей производительности, так как в процессе сварки задействуется один либо несколько проволочных электродов, а также электрод увеличенного сечения.
Теперь рассмотрим главные недостатки электрошлаковой сварки. Первое — этот вид сварки невозможно применить для металлов, толщина которых меньше 16 мм. При этом мы говорим вовсе не об экономической целесообразности, а о невозможности провести сварку именно технически. Второе — для сварки металла от 16 до 40 мм электрошлаковая сварка экономически не оправдана и не окупает себя. Третье — электрошлаковой сваркой возможно производить исключительно вертикальные швы. И последний недостаток — необходимость проведения последующей термообработки при сварке металлов неблагоприятных структур. Термообработка является обязательной для создания необходимых свойств сварного соединения.
4. Газовая сварка. Первый аппарат для газовой сварки был изобретен в далеком 1903 году во Франции. Металл расплавляли при помощи ацетилена и кислорода. Несмотря на то, что первые газовые сварочные аппараты были далеки от совершенства, технология сварки и конструкция сварочных аппаратов практически не претерпели изменений и используются по сей день.
Преимущества газовой сварки:
1. Нагрев и остывание свариваемых поверхностей происходит медленно.
2. Именно при помощи газовой сварки удается достичь наилучшего сваривания таких металлов, как свинец, медь, чугун и латунь.
3. Возможно сваривать металлы с различной мощностью пламени и температурой плавления.
4. Газовая сварка не требует наличия дополнительного источника электроэнергии либо сложного и дорогого оборудования. Это позволяет проводить сварку даже в чистом поле.
5. Сварщик без особого труда может варьировать температурой пламени.
6. Газовая сварка дает возможность не только сваривать металлы, но и закалять, а также резать их.
7. Более высокая прочность швов, получаемых при газовой сварке.
Имеет газовая сварка и свои недостатки, а именно:
1. В отличие от электродуговой сварки, газовая сварка практически не поддается механизации.
2. Большая зона нагрева. Это может привести к повреждению термически неустойчивых элементов, которые находятся недалеко от места сварки.
3. Использование опасных веществ в процессе газовой сварки. В соединении с кислородом эти вещества превращаются во взрывные смеси, которые представляют опасность для здоровья и даже жизни сварщика.
4. Нецелесообразность сварки металлов, толщина которых превышает 5 мм. Это происходит ввиду того, что с ростом толщины металла снижается производительность сварки.
5. Легировать наплавляемый металл при газовой сварке никоим образом не получится.
6. Посредством газовой сварки невозможно сваривать высокоуглеродистые стали.
5. Лазерная сварка. Один из распространенных видов сварки, в процессе которой лазерный луч воздействует на металл очень точечно, приводя к его расплавлению.
Среди преимуществ лазерной сварки выделяются:
1. Минимальный уровень деформации и нагрев деталей.
2. Невысокая трудоемкость (до 20 раз меньше, чем при прочих видах сварки).
3. Возможность использовать лазерную сварку для сваривания разнообразных марок материалов, сплавов и сталей. Титан, медь, высокоуглеродистые марки сталей, стекло, керамика, алмазы и пластмасса – все это очень просто сваривается посредством лазерной сварки.
4. Высокая производительность лазерной сварки.
5. Возможность производить сварку в различных пространственных положениях и труднодоступных местах.
6. Высокое качество сварных соединений.
7. Лазерная сварка позволяет экономить материалы и электроэнергию.
8. Превосходная гибкость процесса сварки. Сварщику не составит большого труда при необходимости осуществить перенастройку на другие режимы сварки.
Если говорить о недостатках лазерной сварки, к ним можно отнести повышенные требования к качеству сборки соединения и необходимость закупки недешевого оборудования, которое по карману не каждому предприятию. Во всем остальном лазерная сварка является одним из лучших способов сварки.
Какой способ выберете вы – решать только вам.
supermontazh.ru
Аргонодуговая сварка: технология производства соединений
Выполнение сварочных работ сегодня попросту необходимо, так как и в быту, и в промышленности, на строительной площадке и во многих других областях необходимость сварочных работ неоспорима. Именно поэтому сварочно-монтажные работы заслуживают внимания. Технологическая сторона соединительных работ – то, что важно знать каждому профессиональному специалисту.
Принципы и технологические моменты соединительного процесса
Технология качественных сварочных работ с газом аргоном основывается на принципе образования электрической дуги между неплавящимся электродом, а также поверхностью обрабатываемого металла. Технические обучение данным работам указывает на то, что электрод помещается в токопроводящем приспособлении горелки, после чего окружают керамическим соплом. Стоит отметить, что расплавление кромок обрабатываемых элементов достигается за счет воздействия дуги, и это основы, о которых нужно обязательно знать.
После этого образовывается единая расплавленная ванна. Если работы ведутся с аргоном, то стоит знать, что данный газ нагнетается в токоведущем приспособлении, и с помощью полученного давления достигается вытеснение кислорода. Технологическая сторона предусматривает, что ванна защищается от азотирования, а также окисления. Дуга сконцентрирована, сжата на малой поверхности, посредством чего достигается высокая температура плавления.
В дугу производится подача присадочного материала, представляющего собой присадочную проволоку, свариваемой с материалом. Несмотря на то, что присадочный материал в общей цепи электрического питания не задействован, получаемый в итоге шов работы аргоном выходит единым, герметичным, а также прочным. Долгое обучение не потребуется.
Технология надежных сварочных работ подразумевает соединительные работы с аргоном, являющимся инертным газом. Следовательно, обучение работам с применением газов должно производиться соответствующим образом.Сварочные процессы могут достигаться при помощи неплавящегося, а также плавящегося электрода. С ролью неплавящегося катода отлично справляется зачастую вольфрамовый электрод.
Соединение аргоном основано на свойстве рассматриваемого газа — не взаимодействовать с химическими свойствами металлов, находящихся уже в расплавленном состоянии, другими газами, выделяющимися в среде горения электрической дуги. Основы знаний, выполнение качественных швов и соединений, а также многое другое получается сделать благодаря такому понятию, как практическое обучение.
Сварочные работы с инертным газом аргоном предусматривают вытеснение более легких элементов из области работ, а поэтому становится возможным качественный результат, изолирование ванны от влияния атмосферы.
к меню ↑Как выполняется?
Обработка деталей аргоном может выполняться в ручном режиме. В таком случае газовая горелка и пруток присадочного материала располагаются в непосредственной близости от рук мастера. Помимо ручного режима,сварочные работы с защитным газом аргоном могут выполняться в автоматическом режиме, предусматривающим перемещение присадочного материала с горелкой около обрабатываемой основы без участия человека.
Упоминая об автоматической обработке аргоном материалов необходимо обращать внимание на то, что выполнение сварочных работ касанием электрода о поверхность изделия практически невозможно. Так, газ рассматриваемого типа имеет достаточно высокий уровень ионизации, а, следовательно, добиться ионизации промежутка дуги довольно сложно. Также технологическая сложность обработки деталей аргоном заключается в том, что от касания электрода с вольфрамовым покрытием дуга загрязняется, после чего интенсивно оплавляется.
В связи с этим технология соединения элементов детали аргоном подразумевает применение специализированного приспособления, которое подключается параллельно к другому источнику питания. Устройство именуется в науке осциллятором. Данное приспособление функционирует по принципу подачи высокочастотных импульсов высокого напряжения на электрод. Импульсы впоследствии приводят к разжиганию электрической дуги посредством ионизации промежутка дуги.
В том случае, если сварочные работы производятся в условиях переменного тока, то осциллятор после ионизации промежутка дуги функционирует в качестве стабилизатора, подающего на дугу импульсы на протяжении смены полярности. За счет этого полезного качества осциллятора достигается технологическая стабильность дуги.
Стоит отметить, что заказы на аргонодуговые сварочные работы весьма требовательны к соблюдению всех тонкостей, сопутствующих сварке аргоном. Также процедура соединения должна предусматривать такое понятие, как технологическая карта, относительно которой также стоит поговорить.
к меню ↑О технологической карте
Многие люди, проходившие обучение в технических учебных заведениях, помнят о том, что такое технологическая карта? Для тех людей, которые запамятовали данное понятие, либо не проходили обучение, стоит напомнить, что технологическая карта представляет собой стандартизированный документ, в котором имеются все требуемые процедурой сведения, инструкции для персонала.
Рассматриваемая карта нужна для получения ответов на вопросы, касающиеся операций, необходимых для выполнения, последовательности выполнения операций, периодичности выполнения операций, результата проведенных работ, временных затрат, нужного инструментария, материалов и др.
Стоит обратить внимание на то, что технологическая карта должна в обязательном порядке сопутствовать качественному и правильному выполнению по соединению металлических элементов. Данная карта содержит все необходимые пункты, регламентирующие правильность производства работ. Карта содержит информацию, которую требует технологическая сторона.
Выполнение всех правил, норм, пройдя качественное обучение работам, становится возможным получение качественного и полезного опыта, который сможет пригодиться в будущем. Технология производства соединений и швов, карта также не должны оставаться в стороне.
Похожие статьиgoodsvarka.ru
www.samsvar.ru
3. Разработка технологического процесса сварки
Разработка технологического процесса сварки включает в себя:
выбор типа сварного соединения;
определение оптимального режима сварки и оборудования;
определение порядка наложения сварных швов.
Основным этапом разработки технологического процесса сварки является выбор типа сварного соединения (односторонний или двухсторонний сварной шов, стыковой или угловой шов) и выбор формы раздела кромок под сварку.
Выбор режима сварки предполагает определение совокупности характеристик сварочного процесса, обеспечивающих получение сварного шва заданного размера, формы и качества. При сварке открытой дугой такими характеристиками являются:
марка и диаметр электрода;
напряжение дуги;
сила сварочного тока;
род тока;
время сварки.
Определив род тока, напряжение дуги и силу сварочного тока можно выбрать необходимое оборудование. (Примечание: В данной работе не предполагается выбор рода тока и типа оборудования).
Важным этапом разработки технологии сварки заданной конструкции является определение порядка наложения швов. Правильный выбор технологии позволяет уменьшить коробление конструкции или появление опасных внутренних напряжений. (Однако эта часть разработки технологии также не входит в задачу данной работы).
4. Порядок выполнения работы
Выбор режима сварки это один из основных этапов подготовки технологического процесса, который определяет качество и производительность сварки. При ручной дуговой сварке основными параметрами режима сварки являются: напряжение дуги в вольтах (U), диаметр электрода в миллиметрах (d), сварочный ток в амперах (I), и скорость сварки в метрах в час (V).
Определение режима сварки начинают с выбора типа и марки электрода и его диаметра. Марку электрода выбирают в зависимости от химического состава свариваемых материалов. Это углеродистые стали, низколегированные и высоколегированные стали. В задании указан вид свариваемого материала, в соответствии с ним из табл. 1 выбирают тип и марку электрода. Диаметр электрода выбирают в зависимости от толщины свариваемого металла. Эмпирически установлено, что диаметр электрода должен быть примерно равен толщине свариваемого металла А.
Сварочный токв зависимости от диаметра электрода определяют по эмпирической формуле:
(1)
где j ‑ коэффициент, равный 50 А/мм;
‑ диаметр электрода, мм.
Напряжение дугидля наиболее широко применяемых электродов в среднем составляет 25…28 В.
Для определения скорости сваркипредварительно вычисляютплощадь поперечного сечения сварного шваи находят из таблиц значениекоэффициента наплавки.
Площадь поперечного сечения сварного шва определяется в зависимости от типа сварного соединения. Различают одностороннее стыковое соединение без скоса кромок, со скосом одной кромки, одностороннее угловое соединение без скоса кромок, со скосом одной кромки, а также двухстороннее стыковое и угловое соединение. При этом технология сварки предусматривает наложение основного наружного шва, а в случае необходимости, внутреннего подварочного шва. Поперечные сечения сварных швов для заданных толщин металла определены в ГОСТ 5264-80. Схематическое изображение некоторых сварного соединения дано на рис 2.
Для углового соединения с наложением основного наружного шва площадь поперечного сечения определяют по формуле
,
мм2(2)
а б
в г
д ж
Рис. 3. Схема стыковых (а — C2, б — C8) и угловых (в — У4, г — У5, д — У6,ж — У7) соединений: 1- основной шов, 2- подварочный шов.
Для стыкового соединения с наложением основного наружного шва площадь поперечного сечения определяют по формуле
,
мм2(2 а)
Здесь — коэффициент увеличения площади,
учитывающий наличие зазора между
частями и выпуклость шва (
=
1,4).
Коэффициент
наплавки(г/А ч), зависит от выбора электрода
величина его указана в табл. 1. Из группы
электродов, обеспечивающих заданные
физико-механические свойства сварного
шва, необходимо выбирать те, которые
дают более высокий коэффициент наплавки
и, следовательно, большую производительность
процесса.
Скорость сваркив (м/ч) определяют из выражения:
,
(3)
где —
сила сварочного тока, А;
— коэффициент наплавки, г/А ч;— плотность металла, (для стали=7800 кг/м3)S — площадь поперечного сечения
сварного шва, мм
Основное технологическое времяв часах, определяется, как
, (4)
где V— скорость сварки в (м/ч),L— длина сварных швов на изделии, мм.
Расход электродов.Зная площадь наплавленного металла, плотность и длину сварных швов, определяют его полную массу
, (5)
где — масса наплавленного металла, г;S— площадь наплавленного шва, мм2;L— длина сварных швов на изделии, мм;— плотность металла, кг/м3.
Расход
электродов с учетом потерь приближенно
принимают равным = 1,6…1,8 от массы наплавленного металла.
(6)
Где — масса металла электродов, г;
Определить количество электродов необходимое на заданную длину сворного шва можно по формуле:
, (7)
где — длинна электрода, мм;( длину электродов
принимаем равной 300 мм)
Результаты расчетов представляют в следующем виде
дуговая сварка сварка стальных листов (указать марку стали )
указать вид сварки (угловая, стыковая)
толщиной ____мм (указать толщину).
длина сварного шва ____мм (указать длину).
Напряжение дуги в вольтах (U),
Сварочный ток в амперах (I),
Скорость сварки в метрах в час (V)
Основное технологическое время сварки в часах (T)
Тип электрода (указать),диаметр электрода в миллиметрах (d), расход электродов в килограммах.
studfiles.net
Технология проведения сварочных работ.
Сварочные аппараты сегодня получили довольно широкое распространение, поэтому информация о технологии проведения сварочных работ будет довольно актуальной.
Основные плюсы работы со сварочным аппаратом
Достоинством сварочных механизмов является их возможность выдерживать высокие нагрузки. Популярность к ним пришла благодаря малой трудоемкости. Также они имеют хороший, высокоразвитый уровень технологии. Для проведения сварочных работ не требуется особой подготовки материалов. Сварочные работы находятся на втором месте по популярности в сфере технологического соединения элементов. Более популярным может быть только соединение с помощью резьбы. Используя сварочный аппарат, вы не только можете сварить новый материал, но и легко подправить деталь, в которой есть мелкие трещинки.
Кроме достоинств этот аппарат имеет и свои недостатки. Агрегат не может обрабатывать целый ряд материалов. Физико-математические особенности разных видов стали не позволяют нормально обрабатывать их сварочным аппаратом, в связи с чем на этих материалах указывается степень свариваемости. Места соединения могут образовывать сильное внутреннее напряжение, в то время как сами швы невозможно нормально контролировать. Хороший результат может получиться только при использовании высокоточного оборудования. По этой причине для качественной работы просто необходима качественная современная техника.
Виды швов
Есть три вида сварочных швов:
- встык – это вид шва, в котором две детали прислоняются друг к другу, и посередине проводятся сварочные работы;
- внахлест – это максимально прочный вид шва, так как вы получаете двойное соединение;
- впритык – вариант удобен тем, что имеет самые тонкие и визуально практически незаметные швы.
Кроме особенностей внешнего вида швы могут делаться на различающиеся по мерам нагрузки. Сегодня встречаются лобовые, фланговые и косые швы. По формам сечения они могут иметь форму равнобедренного или неравнобедренного треугольника. Существуют также выпуклые и вогнутые швы. Если изделие будет испытывать высокие нагрузки, то самым надежным будет выпуклый шов.
Алгоритм сварочных работ
Для проведения сварочные работ и формирования качественных швов необходимо выполнить следующие действия:
- качественная подготовка материала, проведение очистки его от пыли, остатков масла, а также от окалины;
- проведение предварительного осмотра вида шва;
- проведение сварочных работ;
- термическая обработка изготовленной детали;
- проверка шва.
Рекомендации для проведения работ
Существует ряд правил для проведения сварочных работ, о которых не стоит забывать, если вы хотите получить качественное изделие. Шов не должен быть более чем на 1,5 раза толще самого материала. Если вы не выполняете это правило, то шов может создать внутреннее напряжение, что приведет к деформации изделия, что более неприятно — даже разрушить его. Если по завершению работы вы увидели что требование не выдержано, требуется приступить к спецразделке.
Швы, созданные при помощи сварочных работ, должны обеспечить изготавливаемой детали минимальное коробление. Для этого в первую очередь нужно выполнить все параллельные швы, потом приступать к перпендикулярным, а в конце пройтись по контуру. Тогда изготовленное изделие будет служить долго. Не забывайте также, что ребра жесткости для усиления выносливости изделия варятся с переменным направлением. Это говорит о том, что с разных сторон ребра сварку деталей надо делать от разных краев. Так вы сначала варите слева направо, а потом справа налево.
Для повышения технологичности изделий, которые вы варите, надо учитывать некоторые правила, поскольку в этом процессе важна сборка деталей и образование шва:
- детали надо располагать так, чтобы вам было удобно подобраться к ним со сварочным аппаратом. Не стоит проводить образование шва близко к двум деталям, опирающимся на основы конструкции;
- базирование деталей, которые будут поддаваться сварочным работам, должно быть законченным и иметь хорошую надежность. Тщательно продуманное изделие не нуждается в поддержке, дополнительных замерах и корректировании;
- не стоит сваривать толстые детали с деталями тонкими. Это может привести к возникновению напряжения и деформации изделия;
- для создания более качественного изделия нужно минимизировать количество сваренного металла;
- если вы варите замкнутые изделия, есть смысл избежать давления деталей друг на друга. Это может кардинально уменьшить выносливость изделия.
Тонкости сварочных работ
Рассмотрим основные трудности выполнения сварочных швов методом электродуговой сварки. Здесь существует вероятность отклонения дуги. Причиной могут стать электромагнитные силы и потоки воздуха. Об этом не надо забывать при проведении сварочной работы подобным методом.
При завершении надо выдержать электролит до самостоятельного обрыва дуги. При обработке низкоуглеродистых сталей нужно использовать метод сварки в среде защитных газов. Здесь используется смесь газов. Чистым аргоном свариваются только изделия специального назначения.
Все публикации
fs2003.ru
Технологический процесс газовой сварки » Привет Студент!
Сварные швы. Подлежащее сварке место свариваемых изделий должно быть предварительно надлежащим образом подготовлено; такая подготовка обычно заключается в скашивании свариваемых кромок, или, как говорят, в разделке кромок. На фиг. 338 показана наиболее типичная разделка свариваемых кромок.
Скошенные поверхности кромки аб и а’б’ называют скосами и фасками, остающуюся после снятия фаски часть листа бв и б’в’ — притуплением, расстояние вв’ между кромками листа — зазором, а угол А, образуемый фасками, называют углом разделки (или углом скоса кромок).
Сварные швы можно классифицировать по различным признакам. На фиг. 339 приведена схема классификации сварных швов.
Рассмотрим различные типы сварных швов в порядке, соответствующем приведенной схеме.
При сварке встык свариваемые детали помещают рядом. Разделку свариваемых поверхностей определяют толщиной свариваемых деталей и общими условиями работы. На фиг. 340, а показаны различные способы разделки кромок при стыковой сварке. На фиг. 340, б показаны различные схемы тавровых соединений; на фиг. 340,в — соединение внахлестку (этот тип соединения редко применяется при газовой сварке).
На фиг. 341 показаны сварочные швы, получаемые при различных положениях в процессе сварки.
Все показанные на фиг. 341 швы являются непрерывными. В тех случаях, когда нет надобности в плотном соединении и когда это возможно по условиям прочности, шов делают прерывистым. На фиг. 342 показаны прерывистые швы; изображенный на схеме а называют цепным швом, изображенный на схеме б — шахматным.
На фиг. 342, в показан шов, расположенный параллельно действующей на него силе; такой шов называется фланговым. На фиг. 342, г действующая сила направлена перпендикулярно к длине шва; такой шов называется лобовым.
При промежуточном положении сварного шва, когда он расположен под некоторым углом (острым или тупым) к действующему усилию, шов называется косым.
На фиг. 343 показана схема разреза сварного шва. Выступ шва над поверхностью сваренных листов называют усилением, выступ шва на обратной стороне — подваркой или обратной подваркой.
Металл подлежащих сварке деталей называют основным, металл, подаваемый извне и расплавляемый вместе с основным, — присадочным. Присадочный металл после расплавления пламенем газовой горелки (или электрической дугой) образует вместе с расплавленным основным металлом свариваемых кромок металл шва (или наплавленный металл).
Процессы газовой и электрической дуговой сварки, состоящие из расплавления свариваемого и присадочного материала и последующего затвердевания его, являются процессами металлургическими. Все явления окисления и раскисления металла, проникновения в металл примесей и удаления их из металла, рассмотренные в разделе «Металлургия», имеют место и при сварке и отличаются лишь быстротой протекания; кроме того, расплавляемый в процессе сварки металл растворяет в себе газы.
Процессы окисления металла при газовой сварке происходят за счет взаимодействия с кислородом, подаваемым через горелку и поступающим из окружающего воздуха. Восстановительные процессы происходят главным образом за счет окиси углерода и водорода горючих газов.
Присадочный материал. Присадочный материал должен обеспечивать получение металла шва, по механическим качествам близкого к основному материалу. Исходя из этого основного условия, присадочный материал должен удовлетворять следующим требованиям:
1) химический состав присадочного материала должен быть близок к химическому составу основного металла;
2) температура плавления присадочного материала должна быть близка к температуре плавления основного металлаf
3) плавление присадочного материала должно быть спокойным, без разбрызгивания его частиц и не должно давать газовых пузырей и шлаковых включений в наплавленном металле;
4) проволока или прутки присадочного материала должны быть гладкими, чистыми, не должны иметь на поверхности окалины, ржавчины, масла.
Толщина присадочного прутка берется в соответствии с толщиной свариваемых изделий (листов, прокатных профилей и т. п.).
Повышение производительности труда наших сварщиков-стахановцев связано с применением присадочного материала возможно больших диаметров и пользованием горелками больших размеров. Применение прутков большого диаметра требует более внимательной работы сварщика, который должен в этом случае сильнее греть пруток и обеспечивать своевременное расплавление основного металла.
Флюсы. Сварочными флюсами называют вещества, применяемые при сварке металлов для растворения окислов металла и образования легкоплавких и малого удельного веса шлаков.
Свариваемый и присадочный металл всегда в той или иной степени покрыт пленкой окислов; эта пленка утолщается при нагреве металла; она образуется также и на каплях расплавленного металла. Таким образом, окислы металла всегда имеются в сварочной ванне. Окислы металлов имеют высокую температуру плавления и густоплавки. Флюсы растворяют окислы металлов, образуя с ними легкоплавкую жидкотекучую массу, которая всплывает на поверхность сварочной ванны. Освобожденный от неметаллических включений наплавленный металл образует однородную массу, которая при застывании будет всюду иметь одинаковые механические качества.
В качестве флюсов применяют кремнезем, борную кислоту, буру, соду, поташ.
В виде примера рассмотрим взаимодействие закиси железа с применяемым в качестве флюса кремнеземом:
FeSiО3 является шлаком, всплывающим на поверхность сварочной ванны, которая оказывается, таким образом, освобожденной от FeO.
Способы и приемы газовой сварки. Газовую сварку можно осуществлять многими способами с применением различных приемов; на фиг. 344 приведена схема классификации способов и приемов газовой сварки.
По способу передвижения горелки газовая сварка делится на правую и левую.
Во время работы сварщик держит горелку всегда в правой руке, присадочный материал — в левой. Если в процессе работы движение горелки и прутка производят слева направо, сварку называют правой, при обратном направлении движения — левой. На фиг. 345, а показан левый способ сварки, на фиг. 345, б — правый.
При левом способе присадочный пруток идет впереди горелки, при правом впереди идет горелка, которая в последнем случае направлена на наплавленный металл, т. е. в сторону, противоположную движению горелки вдоль шва.
При левом способе в противоположность правому пламя направлено на более холодный основной металл. Для лучшего прогрева металла горелке сообщают, кроме поступательного, и небольшие колебательные перемещения в перпендикулярном к шву направлении.
При правом способе пламя направлено на горячий наплавленный металл; в поперечных движениях горелки почти нет надобности, и нагрев является более сосредоточенным, поэтому при правом способе скорость сварки больше, чем при левом. При правом способе конец прутка присадочного материала может быть все время погруженным в расплавленный металл и расплавляться одновременно с основным металлом, что делает шов более однородным и улучшает его качества. Благоприятно также влияет на качество шва отжиг наплавленного металла направленным на него пламенем. Хорошее использование тепла при правом способе сварки позволяет при небольшой толщине свариваемых листов (до 6 мм) вести сварку без скоса кромок. По этой же причине угол разделки кромок при более толстых листах в случае правой сварки делают меньшим, чем при левой (при левой около 90°, при правой 60—70°). При правом способе сварочный пруток перемещают по спирали, оставляя конец его в ванне расплавленного металла.
Таким образом, правый способ сварки имеет ряд преимуществ перед левым. Можно, однако, отметить, что при сварке листов толщиной менее 5 мм, т. е. с меньшей массой основного металла, левый способ почти равноценен правому.
В зависимости от толщины свариваемых листов наклон горелки и прутка к направлению их движения можно изменять в пределах, указанных (приблизительно) на фиг. 346; чем толще свариваемые листы, тем больше угол наклона горелки к свариваемому листу.
По количеству факелов пламени газовую сварку можно разделить на сварку однопламенной, двухпламенной и трехпламенной горелкой; большие количества факелов пламени практического применения не имеют.
В случае применения двухпламенной горелки одним факелом подогреваются кромки основного металла, а другим ведется самая сварка.
На фиг. 347 показана схема процесса сварки при двухпламенной горелке. При пользовании трехпламенной горелкой одним факелом подогревают кромки основного металла, другим— присадочный пруток, третьим ведут процесс сварки.
Многопламенные горелки применяют лишь при правом способе сварки; применение их позволяет значительно увеличить скорость процесса: на 25—50% против левого способа и на 15—30% по сравнению с правым при пользовании однопламенной горелкой. Применение многопламенных горелок дает 10—20% экономии в расходе горючих газов и кислорода.
Многослойную газовую сварку применяют при особо ответственных работах. Сущность этого способа заключается в том, что сварочный шов получают не сразу, а в несколько проходов: чем толще свариваемые детали, тем больше число слоев шва. Применение многослойной сварки улучшает качество шва, так как каждый нижний слой подвергается отжигу при наложении на него верхнего слоя. Общая скорость получения шва в случае многослойной сварки уменьшается, а расход горючего и кислорода увеличивается.
Сварка двойным валиком. Сущность этого способа заключается в том, что при вертикальном положении свариваемых деталей сварку ведут с обеих сторон шва одновременно. Получаемый при такой сварке шов состоит из двух валиков, расположенных по обе стороны сваренных листов. Схема сварки двусторонним швом или швом с двумя валиками показана на фиг. 348.
Нагрев основного металла с обеих сторон, уменьшая потери тепла, дает экономию газов и увеличивает скорость сварки.
Скачать реферат: У вас нет доступа к скачиванию файлов с нашего сервера. КАК ТУТ СКАЧИВАТЬ
Пароль на архив: privetstudent.com
privetstudent.com
Карта технологического процесса сварки
Проектирование соединительных узлов различного назначения предусматривает расчёт прочности при нагрузках. Воздействие разнонаправленных сил на сварочный шов требует особого подхода, поэтому инженер-проектировщик должен кратко изложить свои требования и донести их до исполнителя.
В сопроводительном техническом задании для этой цели используются карты технологического процесса сварки, в которых отражается способы подготовки кромок, вид и режим работ при соединении деталей и способы обработки шва. Мы расскажем о параметрах и требованиях, входящих в это краткое пояснение.
Разработка технологии сварки при проектировании
Сварочные работы, как и любые металлургические процессы, требуют досконального соблюдения технологической последовательности операций. Прежде чем начинать проектирование этого вида соединений и стыков необходимо произвести расчёт узлов прочности, подобрать материал заготовки, электрода и способ сварки.
На основании анализа таких параметров и согласно ГОСТ, СНиП и другой строительной документации и рассчитывается оптимальное сочетание прочности и долговечности всей металлоконструкции. Весь технологический процесс сварки и сборки деталей, а также дальнейший неразрушающий или иной контроль качества, находит отражение в сопровождающей проект карте.
Каждый проектировщик при разработке должен учитывать эксплуатационные требования к готовому изделию и область его дальнейшего применения. Проектная документация должна иметь соответствующий раздел, где указываются условия и область использования всей конструкции, и способ применяемого сварного соединения, а именно:
- общее назначение конечного изделия или комплекса конструкций;
- условия эксплуатации применительно к температуре, давлению или ветровым нагрузкам;
- размеры и общий вид свариваемых деталей, конструкций или труб с указанием габаритов;
- марки материалов или сплавов, а также разнородных по составу заготовок;
- разделка стыков, температурная подготовка, а также вид сварки и описание газовой инертной или активной среды;
- диаметр и марку электродов или сварочной проволоки.
Все эти данные, отражённые в сопроводительной инструкции, служат для оптимального проектирования и наилучшего понимания исполнителями сути работ. А это может существенно повлиять на качество изготовления каждого конкретного узла.
Такого рода разделы являются результатом труда группы проектировщиков и имеют большое значение, поэтому обязательны к изучению перед началом работ.
Карта подготовительного и сварочного процесса
Для конкретного узла соединения металлов разработан подробный, краткий документ, который является руководством по сварке и подготовке стыка с указанием всех деталей, исключающих двусмысленное толкование процесса работ. Он разработан на основе норм и правил, а также ГОСТов и регламента Проекта Р НОСТРОЙ 12-2014, в котором указаны требования к персоналу, организации рабочего места, условий прокалки и контроля качества.
Непосредственно условия подготовки стыка и технологию сварки расшифровывают в карте сварочного процесса, где описан весь производственный цикл, а именно:
- характеристики основного материала изделия, марка стали, вид сплава или разнородных металлов;
- геометрические параметры заготовок, схема разделки и сборки стыков, а также количества проходов в виде эскизов;
- характеристики слоёв шва с указанием полярности сварки, марки электродов и их диаметра;
- положение сварочного узла в пространстве и пределы допустимой силы тока при прихваточном и послойном прохождении;
- температура и время прокаливания заготовок и электродов;
- способ обработки шва после сварочных работ;
- контроль качества с указанием способа;
- метод исправления дефектов;
- метод сварки и тип оборудования, а также тип проволоки и состав газовой смеси.
Технологическая карта при сварке является руководством к действию и неукоснительно соблюдается исполнителем. От соблюдения процесса зависит конечное качество изделия и его способность служить длительное время в заданном режиме эксплуатации. Особенно значимо чёткое соблюдение технологии в условиях трубопроводов высокого давления на Крайнем Севере или в других районах с экстремальными условиями работы.
Очень важно все возможные изменения режима работ или материала заготовок и электродов согласовывать с проектной организацией и указывать в сопроводительном паспорте изделия.
Подводим итог
Мы рассказали о таком важном сопроводительном документе, как карта технологического процесса сварки. В нём в сжатой, но оптимальной и доступной форме изложена последовательность работ по соединению металлов и сплавов различными методами. Выполнение технологического цикла исключает брак и позволяет создавать прочное и долговечное конечное изделие.
electrod.biz
Для чего нужна технологическая карта сварочных работ
Реализация проектов в различных сферах производства (строительстве, машиностроении или любой другой сфере) сопряжена с необходимостью последовательного выполнения ряда технологических процедур.
Все условия и порядок выполнения каждой такой процедуры должны быть исчерпывающе описаны в рабочем проекте. Рабочий проект часто представляет собой многотомный документ, содержащий большой объем текстовой и графической информации. Поэтому составляют технологическую карту, которая помогает представить информацию более компактно, сжато и доходчиво.
Она, по сути, является заранее разработанной и утвержденной инструкцией по сварке конкретного изделия.
Назначение
Работа исполнителей с проектной документацией оказывается затруднительной ввиду обилия информации и разрозненности сведений. По этой причине возникает необходимость создания компактного и ёмкого документа, определяющего порядок выполнения той или иной технологической операции в конкретных условиях. Применительно к сварочным процедурам составляется карта технологического процесса сварки.
Выполнение сварочных работ на производстве осуществляют рабочие бригады сварщиков под руководством мастеров.
При выдаче производственного задания на сварку, как правило, чётко документируется объём работ, подробно расписываются условия их выполнения, применяемое оборудование и материалы.
Это помогает рабочему персоналу соблюсти технологию операции сварки, а руководителю среднего звена легко контролировать процесс её выполнения.
Необходимые для этого данные содержит технологическая карта сварки, которая подготавливается технологами предприятия. В этом документе сконцентрирована вся необходимая информация, содержащаяся в рабочем проекте.
Кроме этого, та часть информации, которая присутствует в проекте в виде ссылки на какой-либо ГОСТ, в технологической карте полностью раскрывается и конкретизируется.
То есть, в карте может не указываться номер ГОСТа, требования которого необходимо выполнить, но подробно расписываются сами требования, касающиеся порядка выполнения сварки.
Содержание
Единой формы технологической карты сварки, которой обязаны придерживаться все без исключения организации, не существует.
Поэтому, если предприятие столкнулось с потребностью в таком документе, а какие-либо отраслевые нормы вышестоящих организаций в этой части отсутствуют, технологическую карту сварки можно разработать и утвердить самостоятельно.
Поскольку документ такого рода подлежит обязательному утверждению, карта должна содержать шапку, в которой указываются наименования предприятия и объекта, где планируются сварочные работы.
В разделе изложения технологии все однотипные сварочные швы для удобства следует объединить, снабдив их общим описанием, содержащим исчерпывающую технологическую информацию.
Кроме информации чисто технологического характера, карта может содержать некоторые нормативно-технические данные. К ним относятся количественный и качественный состав бригады, выполняющей работу, а также время выполнения операционного задания.
Также в карте могут быть указаны трудозатраты общего объема работ с разбивкой их на отдельные этапы и обозначением контрольных сроков их выполнения.
Кроме трудозатрат на сварку объекта, может быть приведен общий расчет затрачиваемых ресурсов. К ним относится стоимость электрической и тепловой энергии, расходных материалов, затраты на заработную плату.
Отдельный раздел технологической карты может содержать сведения о мерах безопасности при выполнении сварки, мероприятиях по подготовке рабочих мест.
Данные о сварных соединениях
По каждой группе сварных соединений, выполняемых в процессе сборки объекта, должны указываться следующие технологические данные:
-
информация о материале, из которого изготовлены соединяемые части объекта, включающая марки сталей, их физические и химические особенности;
- данные о необходимости предварительной подготовки деталей к сварке. Если должен быть применен скос кромок, необходимо привести точное описание геометрических характеристик, форму скоса и необходимые значения углов;
- описание применяемой технологии электродуговой сварки и конкретных аппаратов, посредством которых должна быть выполнена сварка. Указывается режим выполнения сварного соединения, перечень применяемых расходных материалов. Например, при применении ручной дуговой сварки указывается марка и диаметр применяемых электродов, ток при котором осуществляется сваривание, если предусмотрена аргонодуговая сварка, приводится форма применяемого электрода, род и полярность тока, расход газа.
Технологическую карту составляют по результатам исследовательской работы, в которую входят расчеты, эксперименты, подбор оптимальных материалов и многое другое.
Существует огромное количество шаблонов, позволяющих упростить составление карты. Разработанная технология не должна противоречить всем существующим нормам и правилам.
svaring.com